The controller hardware is suited in cases where different drives and motion sequences need to be precisely coordinated within a system. It relieves the central programmable logic controller (PLC) and reduces response times.
Ensure seamless, effortless coordination of multiple axes and drives
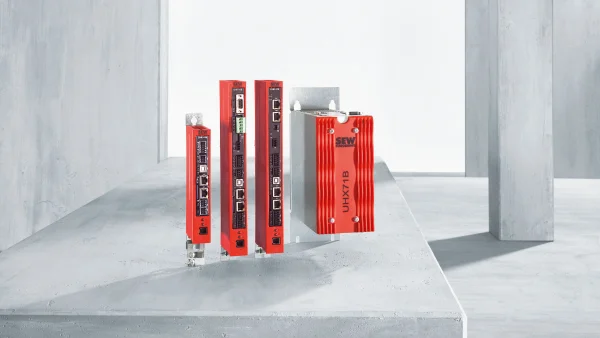
As an operator of complex systems, you need to ensure that different motion sequences, multiple axes, and various drives are precisely coordinated with one another The efficiency of your production depends on this. In order to ensure this required intelligent coordination, you also need both intelligent and reliable control technology.
The control cards from our controller hardware portfolio have been precisely tailored to meet this requirement. Control cabinet installation units are used wherever users are required to implement centrally processed applications.
Thanks to their simple operation and multitude of ready-to-use function modules, they ensure the efficient implementation of motion functions. Their real potential comes to the fore when movements are permitted across multiple axes and need to be coordinated precisely. If the different motion axes within a system are connected via a rapid, synchronous system bus, our recommendation would be to control all motion control tasks via a single controller. Our control technology is ideally equipped for this too. Depending on the performance class, our controllers can handle up to 64 axes using an SBus or SBUSPLUS (system bus with onboard EtherCAT interface). The integrated system bus also allows connection to any of the inverter types in our portfolio.
You can also benefit from the outstanding performance features of our control technology and implement functional and cost-efficient automation for your systems and machines.
You can choose from our different performance levels, each providing optimum control of all motion sequences, depending on your machine and automation requirements:
- DHx21B standard performance class for use as a module controller with motion control functions such as positioning, average response times, and a maximum of 16 axes.
- DHx41B advanced performance class for use as a module controller with high-end, motion-control functions such as electronic gear units, electronic cams and robotics, short response times, and a maximum of 16 axes.
- UHX71B power performance class for use as a module controller or controller for complete automation for demanding motion-control and automation tasks, response times in the 1-millisecond range, and a maximum of 64 axes. The controller can be extended by a second Windows 7 Embedded operating system.
Get in touch with us.
- Our experts understand your industry and requirements.
- Our global network ensures we are there wherever and whenever you need us.
- We have the expertise and the tools to provide optimum advice and support.
Your benefits
-
Any choice of inverter
Thanks to the integrated system bus, which you can use to connect the controller to any type of inverter -
Coordination of multiple axes
A single controller enables intelligent coordination between all axes, thanks to a rapid synchronous system bus -
Efficient automation
Thanks to the performance classes, which allow you to have always the right controller on hand, for simple or high-end motion control
DHx21B control card
Standard performance class
The control card MOVI-PLC® standard is available in the T0 unit version. It can be installed in the MOVIDRIVE® B control cabinet inverter and MOVITRAC® B, but is also available separately as a compact controller:
- DHE21B version with Ethernet interface
- DHF21B version with additional PROFIBUS and DeviceNet slave interface
- DHR21B version with additional PROFINET/EtherNet/IP/Modbus TCP/IP slave interface
Features:
- Motion and logic controller for average response times
- MultiMotion Light motion operating system
- Motion control for up to 16 axes via SBus
- MOVI-PLC® I/O system via SBus
- SD card for easy unit replacement and recipe management
- Rapid engineering via USB and Ethernet
Technical data
- 1 x Ethernet interface (10/100 BaseT) for engineering tasks or TCP/IP and UDP via IEC 61131-3
- 2 CAN interfaces, 1 of which is electrically isolated
- 2 RS485 interfaces, 1 of which is electrically isolated
- USB device
- DHF21B version with PROFIBUS slave DP-V1, DeviceNet slave
- DHR21B version with PROFINET slave, EtherNet/IP slave, Modbus TCP/IP slave
- 8 digital I/Os (inputs/outputs)
- Status display for PLC and fieldbus
- Real-time clock
- 2 MB program memory, 6 MB data memory
- 32 KB retain variables, 24 KB system variables (retain)
- Free-running tasks (min. 10 milliseconds), 1 cyclical task (10 to 10000 milliseconds)
- PC-readable memory card for firmware and application programs
DHx41B control card
Advanced performance class
The control card MOVI-PLC® advanced is available in unit versions T0 to T25. It can be installed with the master module in the MOVIDRIVE® B control cabinet inverter, MOVITRAC® B and MOVIAXIS®. Alternatively, the card can be used on a standalone basis in IP20 housing as a compact controller:
- DHE41B version with Ethernet interface
- DHF41B version with additional PROFIBUS and DeviceNet slave interface
- DHR41B version with additional PROFINET/EtherNet/IP/Modbus TCP/IP slave interface
Features:
- Motion and logic controller for short response times
- MultiMotion Light motion operating system and technology module
- Motion control for up to 64 axes via SBus, or high performance with SBUSPLUS
- MOVI-PLC® I/O system via SBus, or high performance with SBUSPLUS
- SD card for easy unit replacement and recipe management
- Rapid engineering via USB and Ethernet
Technical data
- 1 x Ethernet interface (10/100 BaseT) for engineering tasks or TCP/IP and UDP via IEC 61131-3
- 1x Ethernet interface as SBUSPLUS (EtherCAT®) master
- 2 CAN interfaces, 1 of which is electrically isolated
- 2 RS485 interfaces, 1 of which is electrically isolated
- USB device
- DHF41B version with PROFIBUS slave DP-V1, DeviceNet slave (DHF41B)
- DHR41B version with PROFINET slave, EtherNet/IP slave, Modbus TCP/IP slave
- 8 digital I/Os (inputs/outputs)
- Status display for PLC and fieldbus
- 4 MB program memory, 12 MB data memory
- 32 KB retain variables, 24 KB system variables (retain)
- Free-running tasks (min. 10 milliseconds), 8 cyclical tasks (10 to 10000 milliseconds)
- PC-readable memory card for firmware and application programs
UHX71B controller
Power performance class
The performance class MOVI-PLC® power is available in unit versions T0 to T25. MOVI-PLC® power is an industrial PC with its own slimline, upright housing.
- UHX71B version with Ethernet interface
- UHX71B-OSP71B version with additional PROFIBUS slave interface
- UHX71B-OSR71B version with additional PROFINET/EtherNet/IP/Modbus TCP/IP slave interface
The power performance class provides the ideal solution for centrally processed high-end, motion-control applications with a high number of axes and response times in the 1-millisecond range. The UHX71B compact controller is available as MOVI-PLC® power motion and logic controller and can be freely configured in accordance with IEC-61131-3.